Liquid Membrane Waterproofing
Liquid membrane waterproofing is a modern and effective method used to create a seamless, flexible, and durable waterproof barrier. It involves applying a liquid coating that cures to form a continuous membrane, protecting surfaces from water infiltration and damage.
Key Features:
- Seamless Application:
The liquid coating is applied directly to the surface, ensuring there are no joints or seams where water can penetrate. This seamless nature provides superior protection compared to traditional sheet-based waterproofing methods. - Flexibility:
The cured membrane is highly flexible, allowing it to accommodate structural movements and expansions without cracking or losing its waterproofing properties. This makes it ideal for areas prone to dynamic stress. - Durability:
Liquid membranes are known for their long-lasting performance. They resist weathering, UV radiation, and environmental wear, making them suitable for exposed surfaces like roofs and terraces. - Versatility:Suitable for a variety of surfaces, including concrete, metal, and wood. It can be used in both new constructions and renovations for residential, commercial, and industrial applications
Application Areas:
- Flat Roofs: Provides excellent protection against water pooling and leakage.
- Balconies and Terraces: Ensures these exposed areas remain watertight.
- Basements and Foundations: Prevents water ingress and dampness.
- Wet Areas: Ideal for bathrooms, kitchens, and swimming pools where water exposure is high.
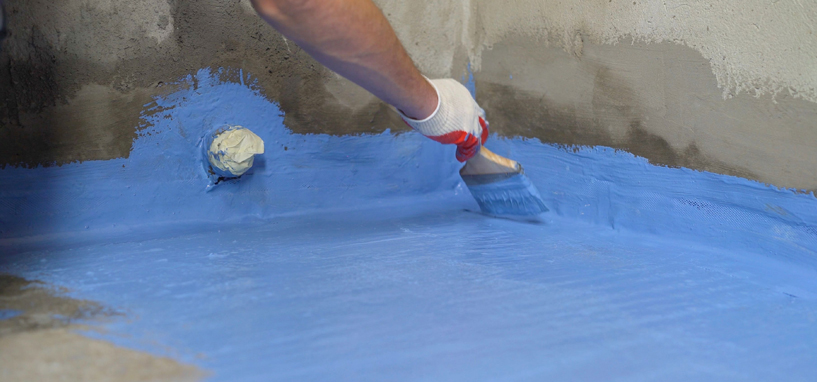
Application Process:
- Surface Preparation:
The surface must be clean, dry, and free from contaminants like dust, oil, and debris. - Primer Application:
A primer may be applied to enhance adhesion of the liquid membrane to the substrate. - Liquid Membrane Application:
The liquid membrane is applied using brushes, rollers, or spray equipment. It can be built up in multiple layers to achieve the desired thickness and protection level. - Curing:
The liquid membrane cures to form a continuous, elastomeric waterproof barrier. The curing time varies depending on the product and environmental conditions.
Advantages:
- Ease of Application: Can be applied quickly and easily, reducing labor and time costs.
- Adaptability: Can be applied to irregular shapes and hard-to-reach areas.
- Maintenance: Easy to inspect and repair if necessary.
Liquid membrane waterproofing is a versatile and reliable solution for protecting structures from water damage, ensuring longevity and structural integrity.
Sheet Membrane Waterproofing
Sheet membrane waterproofing is a traditional and highly effective method used to create a waterproof barrier by applying pre-formed sheets to the surface of a structure. These sheets are typically made of materials like modified bitumen, PVC (polyvinyl chloride), TPO (thermoplastic polyolefin), or EPDM (ethylene propylene diene monomer).
Key Features:
- Pre-formed Sheets:
The waterproofing material is manufactured in sheet form, ensuring consistent thickness and quality. These sheets are then rolled out and applied to the surface. - High Durability:
Sheet membranes are known for their robustness and longevity. They are resistant to punctures, tears, and UV radiation, providing long-lasting protection. - Waterproof Barrier:
They form a continuous, impermeable barrier against water ingress, protecting the underlying structure from water damage. - Versatility:Suitable for a wide range of applications, including roofs, basements, tunnels, and retaining walls.
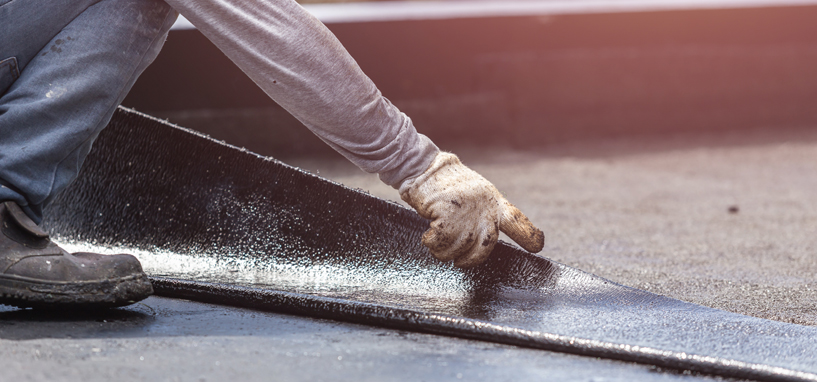
Application Areas:
- Roofs: Commonly used for flat and low-slope roofs due to their ability to withstand standing water.
- Basements and Foundations: Protects against groundwater infiltration and dampness.
- Bridges and Tunnels: Used in infrastructure projects to ensure durability and longevity.
- Balconies and Terraces: Provides a durable, watertight layer for exposed surfaces.
Application Process:
- Surface Preparation:
The surface must be clean, dry, and free from any contaminants to ensure proper adhesion of the sheet membrane. - Primer Application (if required):
In some cases, a primer is applied to enhance the adhesion of the sheet membrane to the substrate. - Sheet Installation:
The membrane sheets are rolled out onto the prepared surface. Overlaps between sheets are sealed using adhesives, tapes, or heat welding to ensure a continuous barrier. - Detailing:
Special attention is given to corners, edges, and penetrations (like pipes and drains) to ensure these areas are properly sealed. - Protection Layer (if required):
In some applications, a protection layer or screed is applied over the sheet membrane to shield it from mechanical damage and UV exposure.
Advantages:
- Consistent Quality: Pre-manufactured sheets ensure uniform thickness and material properties.
- Ease of Inspection: Seams and joints can be easily inspected and tested for integrity.
- Wide Range of Materials: Available in various materials to suit different environmental conditions and project requirements.
Types of Sheet Membranes:
- Bituminous Membranes: Made from modified bitumen and reinforced with polyester or fiberglass. Ideal for roofs and underground structures.
- PVC Membranes: Flexible and easy to install, suitable for roofs and exposed areas.
- TPO Membranes: Known for their heat-weldable seams and resistance to UV radiation, commonly used in roofing applications.
- EPDM Membranes: Highly flexible and durable, often used for large roofs and pond liners.
Sheet membrane waterproofing provides a reliable and durable solution for protecting structures from water damage, ensuring their longevity and integrity in a variety of applications.
Epoxy Coating
Epoxy coating is a type of protective coating that consists of a two-component system: an epoxy resin and a hardener. When mixed together, these components chemically react to form a rigid, durable, and adhesive bond. Epoxy coatings are widely used in various applications due to their excellent protective and aesthetic properties.
Key Features:
- High Durability:
Epoxy coatings provide a tough, long-lasting surface that is resistant to abrasion, impact, and wear. - Chemical Resistance:
They are highly resistant to a wide range of chemicals, including oils, acids, solvents, and alkalis, making them ideal for industrial and commercial environments. - Adhesion:
Epoxy coatings adhere strongly to a variety of surfaces, including concrete, metal, wood, and more, ensuring a stable and secure protective layer. - Aesthetic Appeal:Available in a variety of colors and finishes, epoxy coatings can enhance the appearance of floors and surfaces, providing a glossy, attractive look.
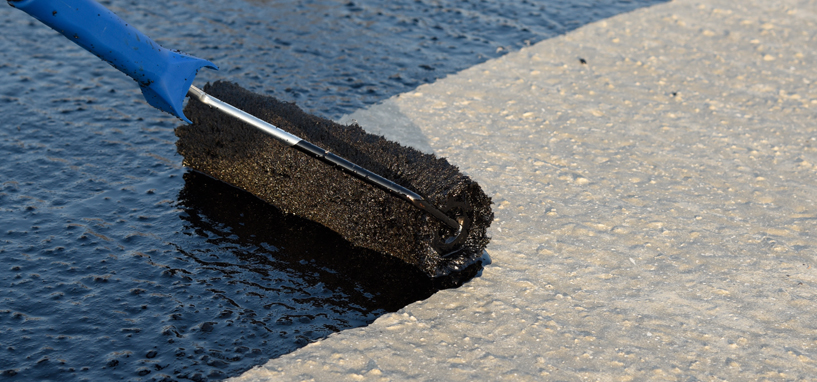
Application Areas:
- Industrial Floors: Warehouses, factories, and manufacturing plants use epoxy coatings to protect floors from heavy machinery, chemical spills, and foot traffic.
- Commercial Spaces: Retail stores, showrooms, and office buildings utilize epoxy coatings for their aesthetic and durable properties.
- Residential Areas: Garages, basements, and kitchens benefit from epoxy coatings for their easy maintenance and appealing finish.
- Marine and Automotive: Used on boats, ships, and vehicles to protect against corrosion and environmental damage.
Application Process:
- Surface Preparation:
The surface must be clean, dry, and free from contaminants like dust, grease, and oils. Surface preparation may involve grinding, blasting, or etching to ensure proper adhesion. - Priming:
A primer may be applied to enhance the adhesion of the epoxy coating to the substrate, especially on porous surfaces like concrete. - Mixing:
The epoxy resin and hardener are mixed according to the manufacturer’s instructions. Proper mixing is crucial for the coating to cure correctly and achieve its desired properties. - Application:
The mixture is applied to the surface using rollers, brushes, or spray equipment. It can be applied in multiple layers to achieve the desired thickness and protection level. - Curing:
The applied coating needs to cure for a specified period, during which it hardens and forms a durable, protective layer. Curing time varies based on temperature, humidity, and the specific product used.
Advantages:
- Durability: Provides a long-lasting protective layer that withstands heavy use.
- Chemical Resistance: Protects surfaces from chemical spills and exposure.
- Easy Maintenance: Epoxy-coated surfaces are easy to clean and maintain.
- Enhanced Appearance: Offers a glossy, attractive finish that can improve the aesthetics of a space.
- Slip Resistance: Can be formulated with additives to enhance slip resistance for safety in wet or high-traffic area
Disadvantages:
- Preparation Time: Requires thorough surface preparation for optimal results.
- Application Conditions: Needs controlled environmental conditions for proper curing.
- Potential for Yellowing: Some epoxy coatings may yellow over time when exposed to UV light, though UV-resistant formulations are available.
Epoxy coatings are a versatile and effective solution for protecting and enhancing a wide range of surfaces, offering both functional and aesthetic benefits.
Remedial Treatment in Waterproofing
Remedial treatment in waterproofing involves repairing and restoring existing structures that are experiencing water intrusion or damage. This process is essential for maintaining the integrity and longevity of a building. Here’s what is typically included in remedial waterproofing treatment:
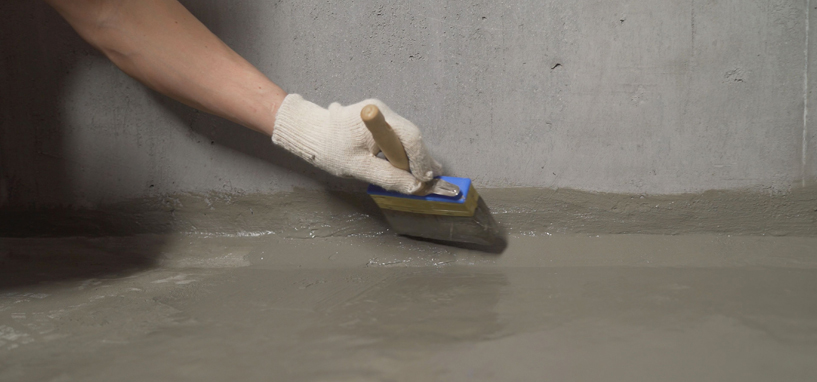
Key Components:
Inspection and Assessment:
- Comprehensive Survey: A thorough inspection of the affected areas to identify the sources and extent of water damage.
- Diagnosis: Determining the underlying causes of water intrusion, such as cracks, faulty construction, or failed waterproofing systems.
Surface Preparation:
- Cleaning: Removing dirt, debris, mold, and old waterproofing materials from the surfaces to be treated.
- Drying: Ensuring the surfaces are dry to facilitate proper adhesion of new waterproofing materials.
Crack and Joint Repair:
- Filling Cracks: Repairing cracks in walls, floors, and ceilings using appropriate fillers or sealants to prevent water ingress.
- Sealing Joints: Resealing joints around windows, doors, and other penetrations to restore their waterproof integrity.
Membrane Replacement or Repair:
- Removing Damaged Membranes: Stripping away old or damaged waterproofing membranes.
- Applying New Membranes: Installing new waterproofing membranes, such as liquid-applied coatings, sheet membranes, or bituminous membranes, to create a continuous barrier against water.
Injection Grouting:
- Chemical Grouting: Injecting chemical grout into cracks and voids to fill gaps and create a watertight seal.
- Cementitious Grouting: Using cement-based grout to stabilize and seal larger cracks and joints.
Exterior Waterproofing:
- Excavation: In cases of severe foundation leaks, excavation around the building’s perimeter may be necessary to access and repair the exterior foundation.
- Waterproof Coating: Applying waterproof coatings or membranes to the exterior foundation walls to prevent future water infiltration.
Drainage Solutions:
- Installing Drainage Systems: Implementing or repairing drainage systems, such as French drains, to redirect water away from the building.
- Slope Correction: Adjusting the landscape grading to ensure proper water runoff away from the structure.
Interior Waterproofing:
- Basement Waterproofing: Installing interior drainage systems, sump pumps, and vapor barriers to manage water that penetrates the foundation.
- Moisture Barriers: Applying moisture barriers to walls and floors to prevent dampness and mold growth.
Protective Coatings:
- Anti-Microbial Coatings: Applying coatings that resist mold and mildew growth, especially in damp areas like basements and bathrooms.
- UV Resistant Coatings: Using UV-resistant waterproof coatings for exposed areas to protect against sun damage and degradation.
Quality Assurance and Testing:
- Leak Testing: Conducting tests to ensure the effectiveness of the remedial waterproofing treatments, such as water spray tests or electronic leak detection.
- Final Inspection: A thorough inspection to confirm all repairs and treatments are completed to the required standard.
Benefits of Remedial Waterproofing Treatment:
- Restored Structural Integrity: Addressing water damage and preventing further deterioration to maintain the building’s structural health.
- Enhanced Property Value: Improving the waterproofing system can enhance the property’s value and appeal.
- Increased Durability: Extending the lifespan of the building by protecting it from ongoing water damage.
- Healthier Indoor Environment: Reducing the risk of mold and mildew growth, which can improve indoor air quality and health conditions.
Remedial waterproofing treatment is essential for addressing existing water damage, restoring the effectiveness of waterproofing systems, and preventing future issues. Properly conducted, it ensures the longevity and integrity of the structure.
Caulking & Sealing Services
Caulking and sealing services are essential for maintaining the integrity and energy efficiency of buildings by preventing air, water, and insect intrusion. These services involve the application of flexible materials to seal gaps, joints, and cracks in various parts of a structure. Here’s what is typically included in caulking and sealing services:
Key Components:
Inspection and Assessment:
- Site Survey: A thorough inspection of the building to identify areas where caulking and sealing are needed, such as windows, doors, joints, and cracks.
- Material Selection: Choosing the appropriate type of caulk or sealant based on the material and location, such as silicone, polyurethane, or acrylic latex.
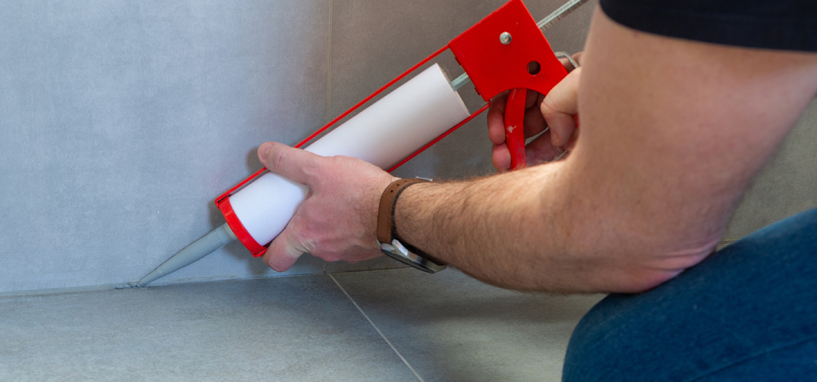
Surface Preparation:
- Cleaning: Removing dirt, dust, old caulk, and debris from the surfaces to ensure proper adhesion.
- Drying: Ensuring the surfaces are dry, as moisture can affect the bonding of the sealant.
Application of Caulk or Sealant:
- Gaps and Joints: Filling gaps and joints around windows, doors, baseboards, and trim to prevent air and water leakage.
- Cracks: Sealing cracks in walls, ceilings, floors, and foundations to enhance structural integrity and prevent water intrusion.
- Special Areas: Sealing around plumbing fixtures, vents, and other penetrations to prevent leaks and drafts.
Tooling and Smoothing:
- Tooling: Smoothing the applied caulk or sealant to ensure a neat and professional finish, enhancing both the appearance and effectiveness of the seal.
Final Inspection:
- Quality Check: Conducting a final inspection to ensure all areas are properly sealed and the work meets the required standards.
Specific Areas of Application:
- Windows and Doors:
Sealing gaps around frames to prevent drafts, water leaks, and energy loss.
- Bathrooms and Kitchens:
Caulking around sinks, bathtubs, showers, and countertops to prevent water damage and mold growth.
- Basements and Foundations:
Sealing cracks and joints to prevent water seepage and maintain structural integrity.
- Exterior Siding and Trim:
Sealing joints and gaps in siding and exterior trim to protect against weather elements and improve energy efficiency.
- Roofing:
Sealing around roof penetrations like chimneys, vents, and skylights to prevent leaks.
Benefits of Professional Caulking & Sealing Services:
- Enhanced Energy Efficiency:
Reducing drafts and air leaks helps maintain consistent indoor temperatures, leading to lower energy bills.
- Water Damage Prevention:
Proper sealing prevents water intrusion, reducing the risk of mold, mildew, and structural damage.
- Improved Indoor Air Quality:
Sealing gaps and cracks minimizes the entry of dust, allergens, and insects, enhancing the indoor environment.
- Extended Building Life:
Preventing moisture and air infiltration helps maintain the structural integrity of the building, extending its lifespan.
- Aesthetic Improvement:
Professional caulking provides a clean, finished look to joints and seams, improving the overall appearance of the building.
Maintenance and Follow-Up:
- Regular Inspections: Periodic checks to ensure the caulking and sealing remain intact and effective.
- Repairs: Prompt repair of any damaged or deteriorated caulking to maintain the protective barrier.
Caulking and sealing services are crucial for protecting buildings from the elements, improving energy efficiency, and maintaining a comfortable and healthy indoor environment.